Failure Analysis su Valvola di Scarico
NUOVA RUBRICA |Come si è rotto? #01TEC EUROLAB
#01
Failure Analysis su Valvola di Scarico
NUOVA RUBRICA | Come si è rotto?
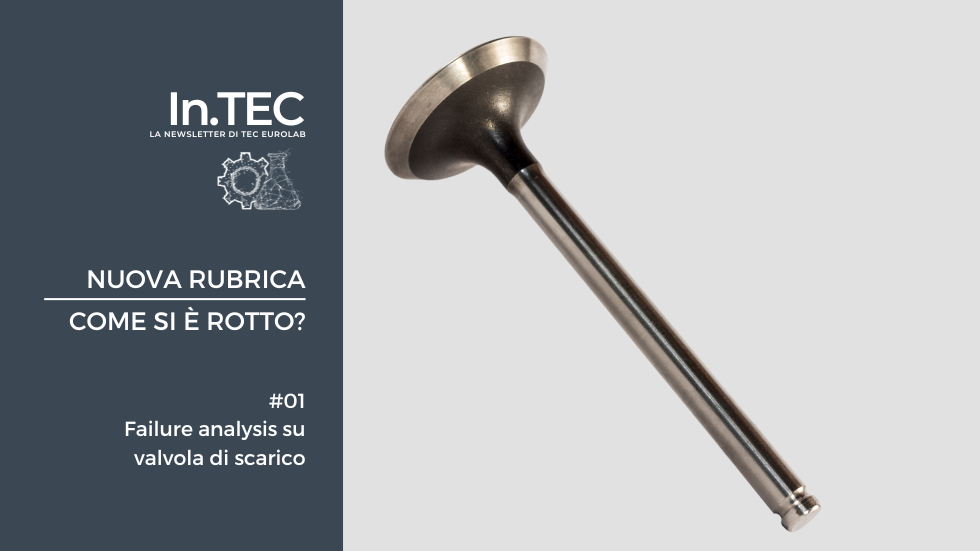
L’oggetto
Una valvola di scarico a fungo è un tipo di valvola utilizzata per controllare e regolare il flusso di fluidi in un sistema. La sua struttura somiglia a quella di un fungo rovesciato, con un corpo cilindrico e una sezione superiore a forma di cupola. La parte superiore, detta “cappuccio a fungo”, è collegata a un’asta che, quando viene azionata, solleva o abbassa il cappuccio per aprire o chiudere il passaggio del fluido.
Queste valvole sono comunemente utilizzate in diversi settori industriali, come il settore petrolchimico, il trattamento delle acque, l’industria alimentare e molte altre applicazioni che richiedono un controllo del flusso del fluido.
Tuttavia, come qualsiasi componente meccanico, le valvole di scarico a fungo sono soggette a possibili modalità di failure. Alcune delle principali cause di guasti possono includere:
- Blocco o ostruzione: Diversi fattori, come sedimenti, particelle o impurità presenti nel fluido, possono accumularsi nella sede della valvola o nell’asta del cappuccio a fungo, causando un blocco del movimento e impedendo il corretto funzionamento.
- Usura e corrosione: L’usura delle superfici di contatto e la corrosione possono compromettere la tenuta della valvola, causando perdite indesiderate e un controllo inadeguato del flusso.
- Rottura dell’asta: L’asta che solleva e abbassa il cappuccio a fungo potrebbe rompersi a causa di sforzi eccessivi, materiali di scarsa qualità o difetti di fabbricazione.
- Malfunzionamento del sistema di controllo: Nel caso di valvole automatizzate, il sistema di controllo elettronico o pneumatico potrebbe guastarsi, portando a un funzionamento improprio della valvola.
- Danni meccanici: Eventuali urti o impatti fisici possono causare danni alla struttura della valvola, compromettendo la sua integrità e il suo funzionamento.
- Problemi di tenuta: Una tenuta insufficiente tra il cappuccio e il corpo della valvola può provocare perdite e influire sulla regolazione del flusso.
Per evitare tali failure, è essenziale eseguire controlli regolari, manutenzione preventiva e utilizzare materiali di alta qualità e adatti all’applicazione specifica. Un’adeguata formazione del personale sull’uso corretto delle valvole e la gestione corretta dei fluidi contribuiscono anche a prevenire incidenti e garantire un funzionamento sicuro ed efficiente delle valvole di scarico a fungo.
Scopo dell’indagine
Lo scopo dell’indagine e l’analisi del danneggiamento del campione identificato come “VALVOLA SCARICO”. Sono eseguite analisi per caratterizzare il materiale e individuare le modalità di rottura, ipotizzando le possibili cause. Le uniche informazioni disponibili riguardano le condizioni in cui è avvenuto il danno, durante l’utilizzo del campione.
Le analisi
Il campione è stato sottoposto a diverse analisi per comprendere il danneggiamento avvenuto. Inizialmente, un esame visivo ha rivelato la rottura di una porzione del fungo.
La superficie di rottura mostrava una generalizzata contaminazione/ossidazione superficiale, probabilmente dovuta alle condizioni di esercizio della valvola a contatto con i gas di combustione. Si sono riscontrati anche segni di propagazione di un meccanismo affaticante.
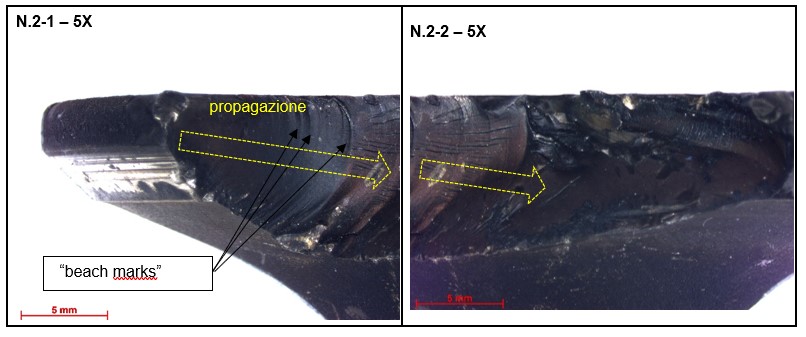
Fig. 1 – ANALISI DEL DANNEGGIAMENTO: Esame visivo
Successivamente, l’analisi frattografica al microscopio elettronico ha confermato una rottura di tipo transgranulare piatta con striature, tipica di una rottura a fatica. La presenza di sostanze esogene, come zolfo e fosforo, legate all’atmosfera di esercizio, è stata osservata sulla superficie di rottura mediante analisi EDS.
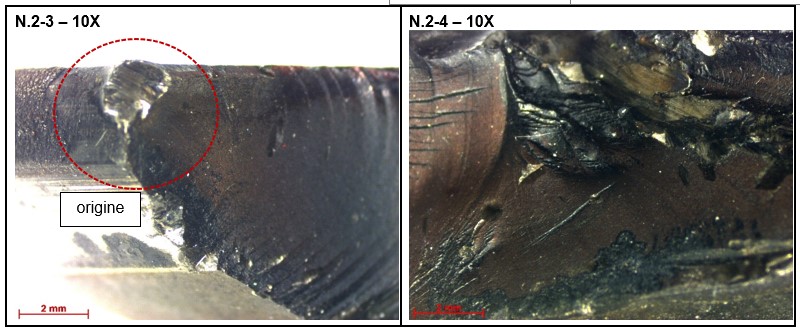
Fig. 2 – ANALISI DEL DANNEGGIAMENTO: Esame visivo
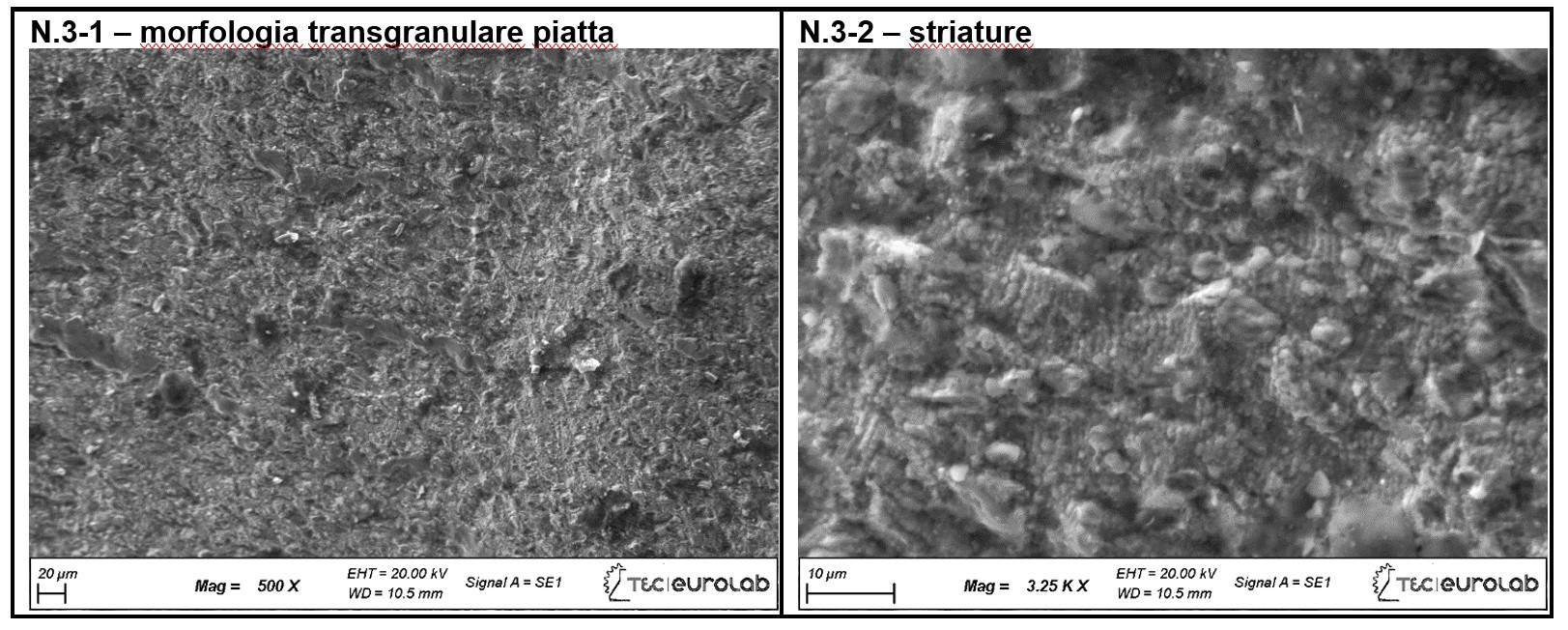
Fig. 3 – ANALISI DEL DANNEGGIAMENTO: Esame frattografico (SEM/EDS)
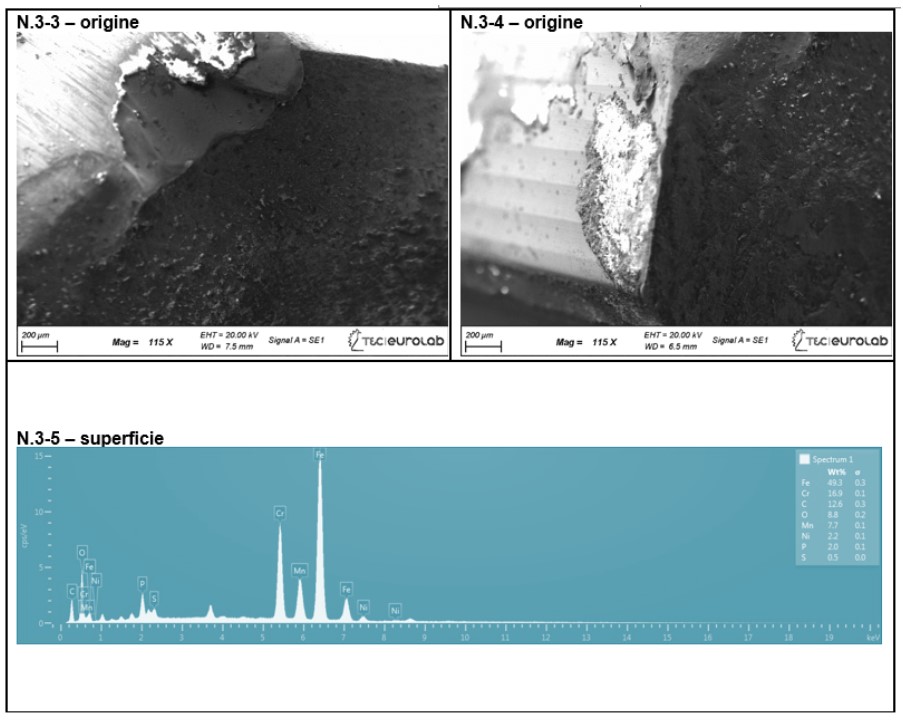
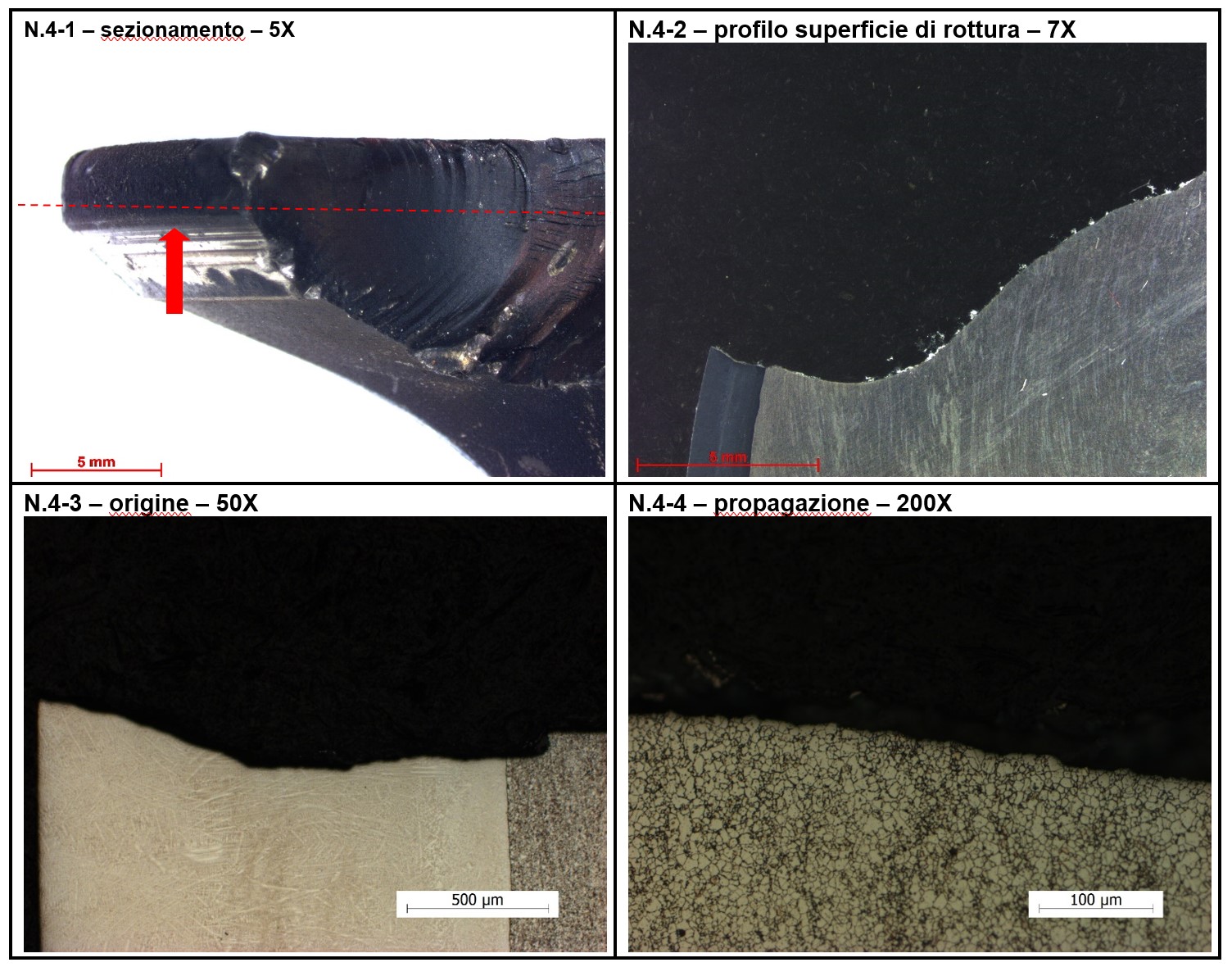
Inoltre, un esame micrografico ha mostrato una superficie di rottura liscia e piatta, attraversante anche il riporto presente sulla circonferenza esterna. Non sono stati rilevati difetti o anomalie correlabili alla rottura.
Fig. 4 – ANALISI DEL DANNEGGIAMENTO: Esame micrografico
Le analisi chimiche hanno classificato il materiale del campione come un acciaio inossidabile austenitico per valvole secondo la norma UN IEN 10090.
L’analisi micrografica ha confermato la presenza di un riporto applicato a caldo con una microstruttura dendritica, mentre la microstruttura del materiale base mostrava una dispersione di carburi, nitruri e carbonitruri in una matrice metallica austenitica, tipica di un acciaio inossidabile austenitico indurente per precipitazione. Il riporto è stato identificato come una lega cobalto-cromo del tipo “stellite.”
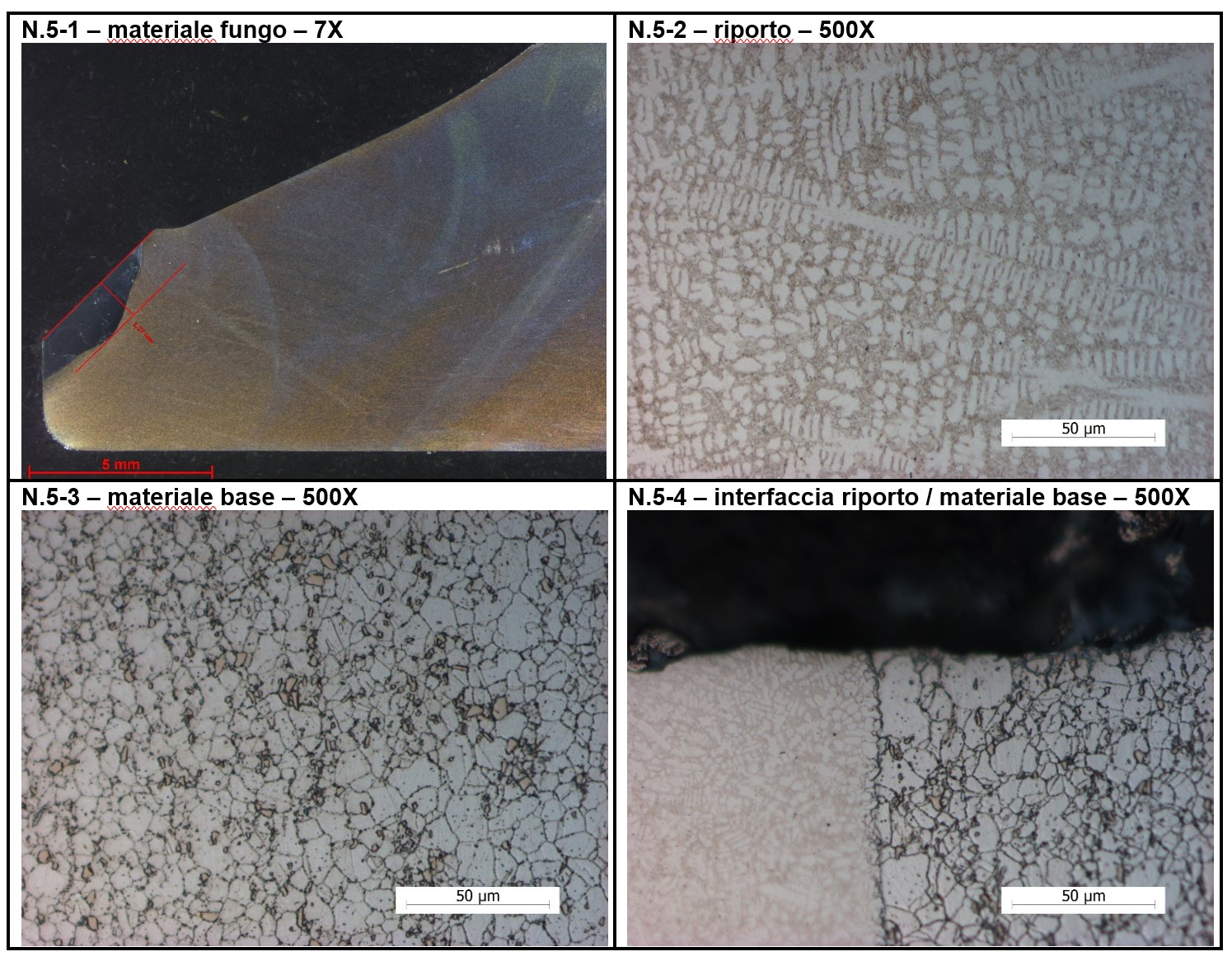
Fig. 5 – ANALISI DEL MATERIALE: Esame micrografico
I risultati
- Il campione risulta privo di difetti microstrutturali, con una durezza di 313 HV per il materiale base e 534 HV per il riporto.
- La rottura è stata confermata come una propagazione a fatica che si è originata nella superficie esterna circonferenziale del fungo, ma non sono stati trovati segni di innesco del meccanismo affaticante.
- Nonostante alcune limitazioni nell’analisi dell’origine dovute a schiacciamenti e danneggiamenti secondari, tutte le analisi concordano sull’origine della rottura per propagazione a fatica senza difetti o anomalie locali rilevanti.
Conclusioni
Il campione analizzato non presenta difetti o anomalie metallurgiche, anche se i requisiti di qualità applicabili non sono noti. I materiali utilizzati, le loro caratteristiche e la conformazione sono tipiche per questo tipo di prodotto.
La rottura è stata causata da fatica, che per questo tipo di prodotti è spesso associata a condizioni locali difettive o a esercizio in condizioni molto severe, soprattutto ad alte temperature, che influenzano significativamente le proprietà di resistenza a fatica.
Vuoi scoprire perchè il tuo componente si è rotto?
Compila il form e sarai ricontattato dal nostro staff tecnico
Leggi gli altri case study sulla Failure Analysis
No Results Found
The posts you requested could not be found. Try changing your module settings or create some new posts.
Il tuo componente si è rotto in esercizio e vuoi capire qual è la causa della rottura?